UTS Faculty of Design, Architecture and Building offers a number of innovative facilities, from the first of its kind in a university, whole-garment knitting machine in the Knit Lab to the cutting-edge robotic technology of the Advanced Fabrication Research Lab.
Pioneering research translation
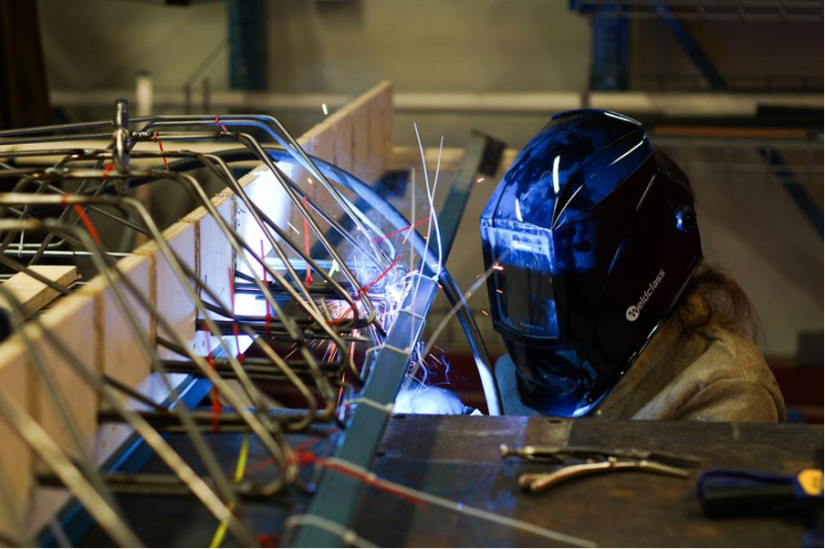
Recent winner of the 2024 UTS Research Translation Award for Knit3D, the UTS Faculty of Design, Architecture and Building (DAB) boasts fantastic facilities including the Sewing Studio, the Fashion Studio, the Digital Maker Space, the Architecture Studio, the Knit Lab and the Advanced Fabrication Research Lab to name a few.
The RES Hub team recently joined Fabrication Workshop Manager, Greg Martens, who explained how the Faculty is very big on studio-based learning.
“Most of our academics are in professional practice, so they’re current with what goes on in the real world and they bring that expertise in to work on real world projects,” he said.
Leaders in fashion design
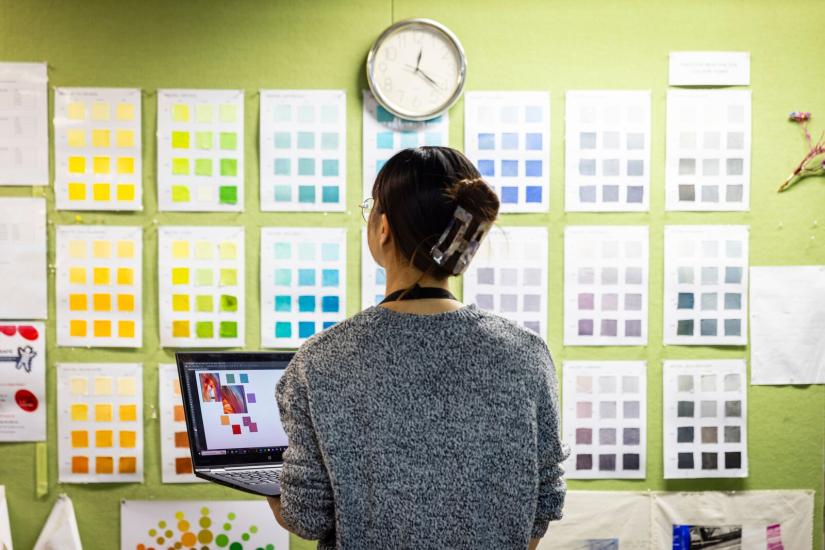
“UTS is number 2 in Australia for fashion and in the top 20 globally,” Greg noted.
Research projects currently in the works include Linda Matthews’ research in DAB’s textile print area to test disruptive patterns for defence. Her project is experimenting with patterns that aim to confuse and remain undetected by drone cameras.
Greg described how the Fashion Studio’s textile print area is very much a place for experimentation.
“Start with a blank canvas and fashion students will explore colour, texture, finish and put them all together to see what you get.”
UTS is number 2 in Australia for fashion and in the top 20 globally.
DAB’s annual end-of-year fashion show welcomes industry guests with most of the audience from professional practice.
Attend the UTS Fashion & Textiles Honours 2024 Graduate Showcase
Interested in getting involved? All welcome to attend the UTS Fashion & Textiles Honours 2024 Graduate Showcase on Wednesday 27 November 6:30pm in the open space in Building 1, Level 5 just outside RES Hub’s rear entrance.
Experience the debut of Australia's future fashion trailblazers as they unveil their cutting-edge designs. Join us for an inspiring showcase of fresh ideas and unique styles, giving you a glimpse into the future of fashion.
Towards sustainable fashion futures
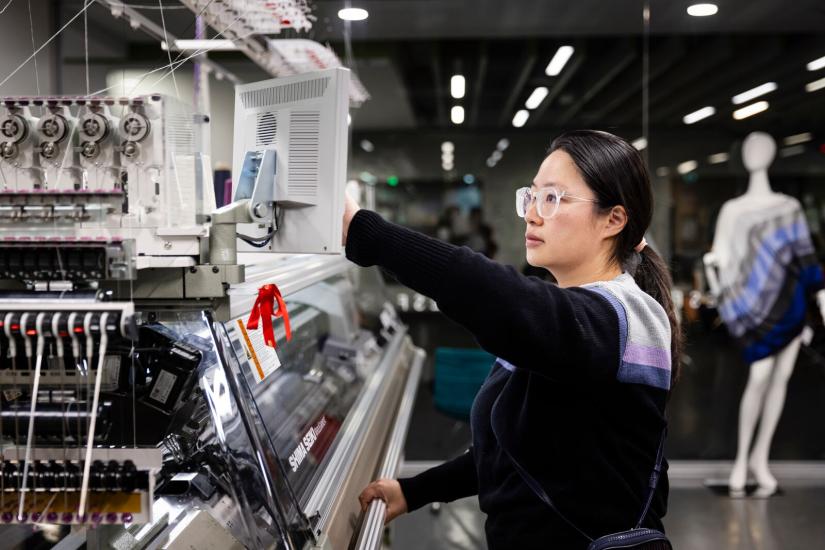
The latest model Shima Seiki WHOLEGARMENT knit machine pushes the boundaries of traditional fashion and textiles, allowing seamless whole garment creation with almost zero waste and off cuts. Think of a 3D printer but with textiles.
The first of its kind to be installed in a university setting anywhere in the world and the only machine in the Southern Hemisphere, Greg said that the machine has generated amazing research opportunities at UTS.
The core team has worked together for seven years, successfully delivering multiple industry-funded, climate-focussed advanced fabrication research projects with partners from Defence, Health, Green-Facades, Workplace and product design.
That’s what research translation is about. How other industries can add value to what other businesses have.
Academic Lead for Seamless Knitting Research and Senior Lecturer in the School of Design, Dr Nga Wun (Doris) Li, plans to utilise the machine as part of a research project to create seamless compression stockings that prevent deep vein thrombosis.
3MT finalist and PhD student, Wajiha Pervez, is also using the machine for her research into developing sustainable athleisure wear.
“It’s not just about fashion. It’s architecture. There's product design. There's health, there's medical, there's automotive,” Greg explained.
The machine has opened doors for experimenting in fabrication in areas such as sport, by using a conductive yarn to measure body performance. Technical expert, Shirley Tam sources the different yarns globally, with plans to source fibres such as fibreglass fibre, graphene fibre and carbon fibre to expand the possibilities of their research.
The team have also worked with Jumbunna to introduce different ways of replicating art to remote First Nations communities.
Associate Professor David Pigram said in his speech for the Research Translation Competition, “Our solution avoids the pain of producing knittable designs unlocking the technology for industries beyond fashion and users beyond experts.”
In a novel new development, the machine is now being used in building fabrication.
Greg explained how multi-disciplinary teams are creating a knitted formwork for designs which are then filled with concrete to create structures such as furniture and air conditioning systems. The traditional method may take 5 or 6 hours compared to just one hour with the knit machine.
“It speeds the process up and also eliminates some of those more traditional manufacturing processes, while also reducing climate change issues,” Greg said. “That’s what research translation is about. How other industries can add value to what other businesses have.”
Dave emphasised the potential global impact of their practice, “Global survival relies on humans using less material, producing less waste and achieving higher performance. We can help.”
Transformative innovation through robotics
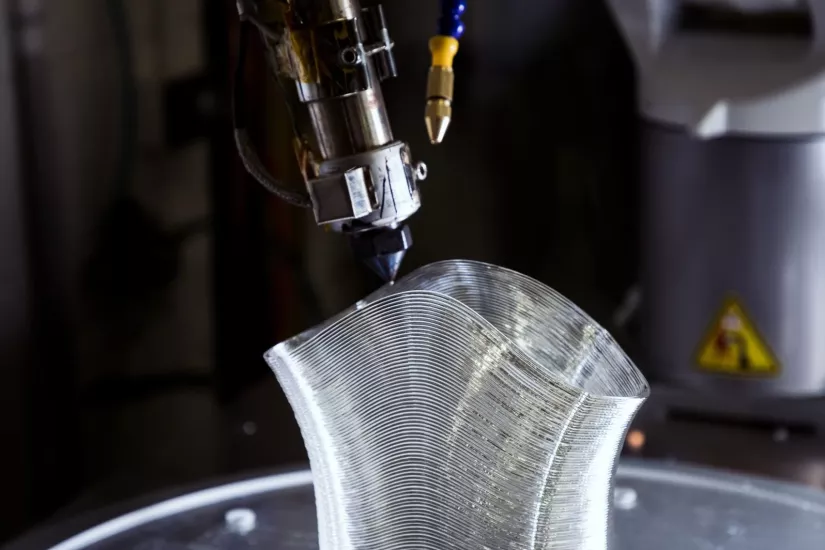
The Advanced Fabrication Research Lab (AFRL) is a research-led space that provides state of the art facilities for the production of artefacts and prototypes using the latest and most advanced digital tools, software and machines.
Since its inception in 2014, the AFRL has supported research, teaching and commercial activities and has become a leader in the fabrication of bespoke artefacts through its continuous collaboration with academics and industry partners on cutting edge research.
It’s opening up more opportunities for other businesses and manufacturers.
For example, DAB has partnered with BVN on a research project called Systems Reef 2 to 3D print an air conditioning system using recycled plastic. The system was built by the KUKA KR Robots in the AFRL and uses organic shapes to increase airflow.
The system is made of 100% recycled plastic that is 3D printed into tubes and produces 90% less embodied carbon than standard air-conditioning systems. Plastic can also be recycled multiple times whereas traditional air-conditioning units are sent to landfill.
BVN and UTS were awarded Best Green Building Material/Product at the Australian Sustainability Awards 2022 for this novel design.
Traditionally used for fabrication, the robot has also been used to experiment in filmmaking and generating new ways of filmmaking by combining two robots.
Remote video URL
Robotics Technical Officer, Tran Dang, was sent to Japan by UTS to learn the complicated software. He is now trying to manipulate the software to be more accessible to students, academics and industry partners.
Greg pointed out that these kinds of collaborations are opening up more opportunities for other businesses and manufacturers.
“Tran is also trying to prove you don’t have to be a knitter to use the software,” he added.
Wild Futures : an architecture and science collaboration
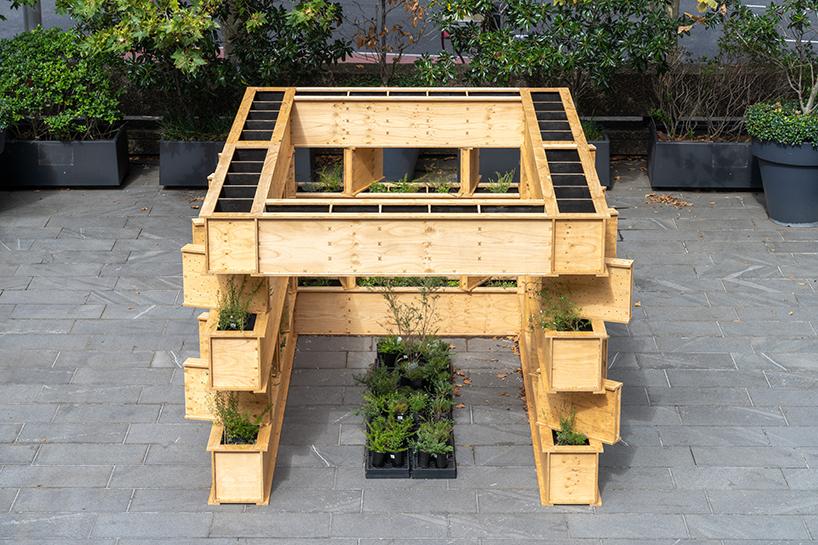
Greg explained the ideas behind a structure called ‘Wild Futures’, a pavilion currently on display in the DAB courtyard.
Produced in the Advanced Fabrication Research Lab, ‘Wild Futures’ pavilion is a collaboration between the Faculty of Science and DAB.
Created by Rafael Luna, Senior Lecturer at UTS, and the director of the Infra-Architecture Lab and Dr Yvonne Davila, a Senior Lecturer in Environmental Biology in the School of Life Sciences, Faculty of Science, the pavilion seeks to create a blueprint for sustainable architecture.
Together with respective architecture and science backgrounds, Rafael and Yvonne are testing a new house prototype for a structure that can help sustain biodiversity by preserving and restoring urban pollinator networks within an urban context.
“The concept is you could build a house or any sort of structure where that's the interior, and then you line the interior to make it look like you're in a home," Greg explained.
With the end goal to develop a prefabricated, modular, two story design of about 160 square metres that can be constructed for around $100k, Rafael and Yvonne are making urban living greener and more sustainable.
Discover DAB
With the Federal Government’s manufacturing agenda expressed in its Future Made in Australia strategy, DAB is well placed to partner with industry to deliver innovations in health, engineering, fashion and sustainability, particularly by using its state-of-the-art seamless knitting technology combined with AI.
Follow DAB in LinkedIn to keep up to date with exciting projects underway, from zero-waste clothing from zero waste yarn, wearable sensors and garments for astronauts and Formula 1 drivers to applications for use in furniture, architecture, building and agriculture.
Discover DAB workshops and resources.